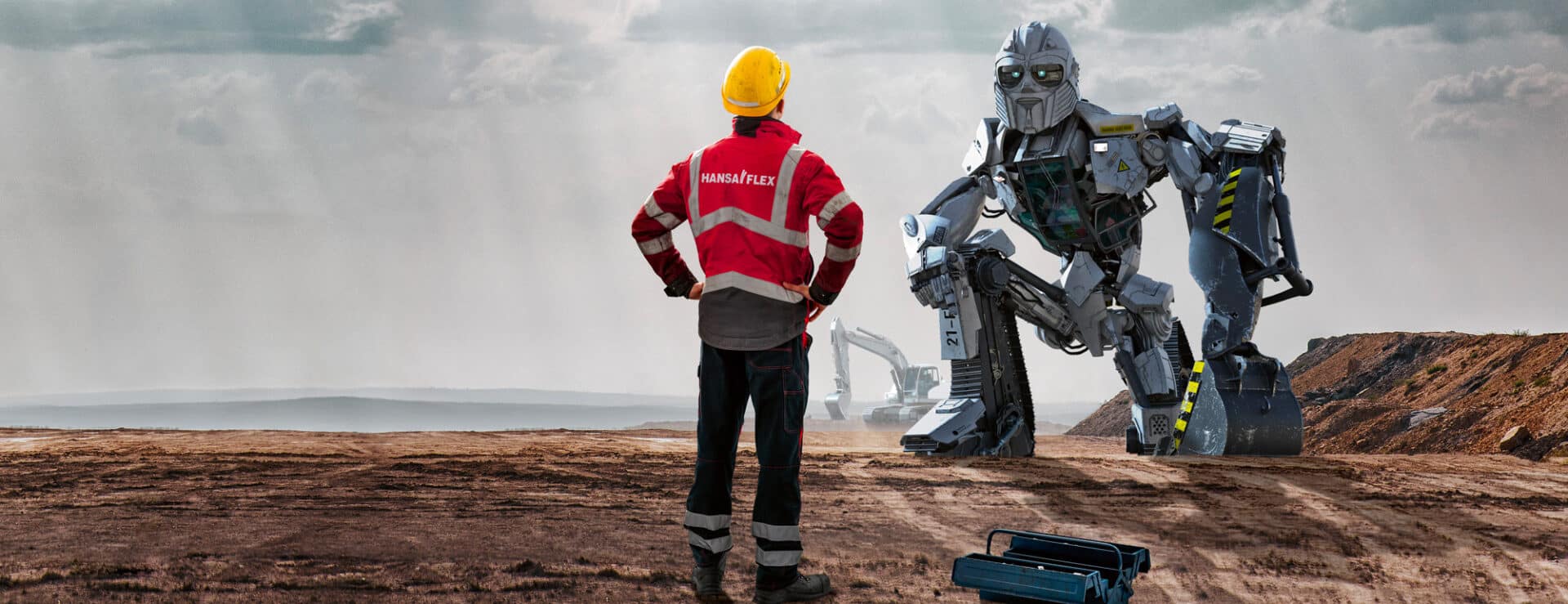
FAQs
Erfahren Sie, wie Hydraulik und Pneumatik verschiedene Industrien mit effizienter und präziser Energieübertragung antreiben. Entdecken Sie die Vorteile, Anwendungen und Wartungstipps beider Systeme für optimale Leistung. Erfahren Sie mehr über die wichtige Rolle von Hydraulikdichtungen und wie Sie diese auswählen und warten können, um eine langanhaltende Zuverlässigkeit zu gewährleisten.
Hydraulik
Hydraulik ist ein Antriebs- und Steuerungssystem, das auf der Nutzung von unter Druck stehenden Flüssigkeiten, in der Regel Öl, basiert. Dieses System nutzt die physikalischen Eigenschaften von Flüssigkeiten, um Energie effizient über Leitungen und Schläuche zu übertragen, was es ideal für vielfältige Anwendungen macht, von der Steuerung von Flugzeugklappen bis zum Heben schwerer Lasten durch Bagger.
In einem hydraulischen System pumpt eine Hydraulikpumpe Flüssigkeit in ein geschlossenes System. Der Druck, der durch die Pumpe erzeugt wird, bewirkt, dass die Flüssigkeit auf einen Zylinder oder Motor wirkt, welcher eine Bewegung oder Kraft ausübt. Über Ventile kann der Flüssigkeitsstrom gesteuert und so die Bewegung oder Kraft präzise kontrolliert werden.
Die Hydraulik bietet eine Reihe von Vorteilen: Sie ermöglicht die Übertragung großer Kräfte bei relativ geringem Energieverbrauch und kann sehr präzise gesteuert werden. Die Systeme sind robust und zuverlässig, was sie besonders für schwere Maschinen und Anlagen geeignet macht, die unter anspruchsvollen Bedingungen arbeiten müssen.
Hydraulische Systeme sind in zahlreichen Industrien verbreitet, darunter im Maschinenbau, in der Automobilindustrie, in der Luft- und Raumfahrt, im Bauwesen sowie in der Land- und Forstwirtschaft. Überall dort, wo schwere Lasten gehoben oder präzise Bewegungen benötigt werden, spielt Hydraulik eine zentrale Rolle.
Die Leistung eines hydraulischen Systems wird durch die Parameter Druck und Volumenstrom bestimmt. Der Druck gibt an, welche Kraft das System ausüben kann, während der Volumenstrom die Geschwindigkeit angibt, mit der es arbeiten kann. Die Gesamtleistung ergibt sich aus dem Produkt von Druck und Volumenstrom.
Hydraulikservice
Bei HANSA-FLEX sind wir stolz darauf, eine umfassende Palette von Hydraulikdienstleistungen anzubieten, die auf die Bedürfnisse unserer Kunden zugeschnitten sind. Unsere Dienstleistungen reichen von der Bereitstellung von hochwertigen Hydraulikkomponenten bis hin zur Unterstützung bei der Installation, Wartung und Fehlerbehebung. Hier sind einige unserer wichtigsten Dienstleistungen:
• Bereitstellung von Hydraulikkomponenten: Wir liefern eine breite Palette von Hydraulikprodukten, darunter Hydraulikschläuche, Armaturen, Verschraubungen, Pumpen, Zylinder und vieles mehr.
• Montage von Hydraulikschläuchen und -systemen: Unser erfahrenes Team bietet professionelle Montageleistungen, um sicherzustellen, dass Ihre Hydrauliksysteme korrekt installiert und optimal konfiguriert sind.
• Wartung und Inspektion: Wir bieten regelmäßige Wartungs- und Inspektionsdienste an, um die ordnungsgemäße Funktion Ihrer Hydrauliksysteme zu gewährleisten und potenzielle Probleme frühzeitig zu identifizieren.
• Reparatur und Fehlerbehebung: Bei Ausfällen oder Problemen stehen unsere Techniker bereit, um schnelle und effektive Reparaturen und Fehlerbehebungen durchzuführen.
• Technische Beratung und Support: Unser technisches Team bietet kompetente Beratung und Unterstützung bei der Auswahl von Komponenten, Systemdesign, Problemlösung und anderen technischen Fragen.
• Notdienst: Wir bieten einen 24/7 Notdienst an, um bei dringenden Problemen
oder Ausfällen schnell eingreifen zu können.
Unser Ziel bei HANSA-FLEX ist es, unseren Kunden nicht nur hochwertige Produkte, sondern auch erstklassigen Service und Support zu bieten. Egal, ob Sie ein komplexes Hydrauliksystem entwerfen oder einfach nur einen zuverlässigen Lieferanten für Hydraulikkomponenten suchen, wir sind hier, um Ihnen zu helfen. Ihre Zufriedenheit und der Erfolg Ihrer Projekte sind unser oberstes Ziel.
Die Wartung von Hydraulikanlagen ist von entscheidender Bedeutung, um deren Leistung, Sicherheit und Langlebigkeit zu gewährleisten. Bei HANSA-FLEX empfehlen wir, dass eine routinemäßige Inspektion und Wartung Ihrer Hydraulikanlagen regelmäßig und mindestens einmal im Jahr erfolgen sollte.
Jedoch hängt die genaue Häufigkeit der Wartung von mehreren Faktoren ab, darunter die Art der Anlage, die Intensität ihrer Nutzung, die spezifischen Betriebsbedingungen und die Anforderungen der jeweiligen Industrienormen oder des Herstellers. In einigen Fällen, insbesondere bei intensiver Nutzung oder bei Betrieb unter harten Bedingungen, kann es ratsam sein, häufiger Inspektionen und Wartungsarbeiten durchzuführen.
Es ist wichtig zu bedenken, dass vorbeugende Wartung weit mehr als nur eine jährliche Inspektion umfasst. Es beinhaltet auch regelmäßige Kontrollen von Flüssigkeitsständen,Temperatur, Druck und Schlauchzustand, sowie den Austausch von Hydrauliköl und Filtern nach den Empfehlungen des Herstellers.
Eine regelmäßige Wartung Ihrer Hydraulikanlagen ist unerlässlich, um eine optimale Leistung und eine lange Lebensdauer sicherzustellen. Es gibt mehrere Anzeichen, die darauf hinweisen können, dass Ihre Hydraulikanlage gewartet werden muss:
• Leistungsminderung: Wenn Ihre Hydraulikanlage nicht die erwartete Leistung erbringt, kann dies ein Anzeichen dafür sein, dass eine Wartung erforderlich ist. Dies könnte sich in einer verminderten Geschwindigkeit, Kraft oder Effizienz äußern.
• Überhitzung: Hydraulikanlagen erzeugen Wärme, aber übermäßige Wärme kann auf ein Problem hinweisen. Wenn Ihre Anlage häufig überhitzt, könnte dies ein Zeichen dafür sein, dass das Hydrauliköl gewechselt oder das Kühlsystem gewartet werden muss.
• Undichte Stellen: Wenn Sie Ölverluste oder Feuchtigkeit um die Anlage herum bemerken, kann dies auf undichte Stellen in den Schläuchen oder Verschraubungen hinweisen.
• Geräusche: Ungewöhnliche Geräusche wie Klopfen, Pfeifen oder Quietschen können auf mögliche Probleme hinweisen, einschließlich Luft im System, verschlissene Komponenten oder unzureichende Schmierung.
• Veränderung der Flüssigkeitsfarbe oder -konsistenz: Wenn das Hydrauliköl trüb wird oder seine Farbe verändert, kann dies auf Verunreinigungen oder Wasser im Öl hinweisen.
• Erhöhter Energieverbrauch: Ein Anstieg des Energieverbrauchs kann darauf hinweisen, dass die Anlage härter arbeitet, um die gleiche Leistung zu erbringen, was auf ein mögliches Problem hindeutet.
Die Kosten für eine routinemäßige Wartung und Inspektion Ihrer Hydraulikanlage können je nach verschiedenen Faktoren variieren. Diese beinhalten die Größe und Komplexität der Anlage, den Zustand der Anlage, die Art und Menge der benötigten Wartungsarbeiten und den Standort der Anlage.
Bei HANSA-FLEX streben wir danach, unsere Dienstleistungen kosteneffizient und wettbewerbsfähig zu gestalten. Wir glauben fest daran, dass präventive Wartung eine kluge Investition ist, die dazu beitragen kann, teure Reparaturen und Ausfallzeiten zu vermeiden, die Leistung und Effizienz Ihrer Anlage zu verbessern und ihre Lebensdauer zu verlängern. Um Ihnen einen genauen Kostenvoranschlag für die Wartung und Inspektion Ihrer Hydraulikanlage zu geben, würden wir gerne mehr über Ihre spezifischen Anforderungen und Bedingungen erfahren. Bitte zögern Sie nicht, uns zu kontaktieren, um einen Termin für eine vor Ort Besichtigung oder eine Beratung zu vereinbaren. Unser freundliches und erfahrenes Team steht Ihnen gerne zur Verfügung, um Ihre Fragen zu beantworten und eine maßgeschneiderte Lösung für Ihre Bedürfnisse zu finden.
Bei HANSA-FLEX sind wir stolz auf unsere Fähigkeit, eine Vielzahl von Hydraulikanwendungen zu bedienen. Obwohl wir eine breite Palette von Branchen und Anwendungen unterstützen, haben wir umfangreiche Erfahrungen und Fachkenntnisse in mehreren speziellen Bereichen.
• Mobile Hydraulik: Wir bieten Unterstützung für mobile Hydraulikanwendungen wie Baumaschinen, Landwirtschaftliche Geräte, Forstmaschinen und Nutzfahrzeuge.
• Industrielle Hydraulik: Unsere Expertise umfasst auch industrielle Hydraulikanwendungen wie Fertigungsanlagen, Automatisierungstechnik und Prozesssteuerungssysteme.
• Marine Hydraulik: Wir unterstützen auch marine Anwendungen, einschließlich Schiffshydrauliksysteme und Offshore-Technologien.
• Spezialhydraulik: Darüber hinaus haben wir Erfahrung mit speziellen Hydrauliksystemen, die unter extremen Bedingungen oder für spezielle Anwendungen konzipiert sind.
Unser Team von erfahrenen Technikern und Ingenieuren ist bestens ausgebildet und verfügt über umfassende Kenntnisse in der Hydrauliktechnologie. Wir arbeiten eng mit unseren Kunden zusammen, um ihre spezifischen Anforderungen zu verstehen und individuell angepasste Lösungen zu entwickeln, die auf ihre einzigartigen Bedürfnisse zugeschnitten sind.
Die Wartung einer Hydraulikanlage bei HANSA-FLEX ist umfassend und sorgfältig darauf ausgelegt, sicherzustellen, dass Ihre Systeme optimal funktionieren und eine lange Lebensdauer haben. Hier ist ein Überblick über das, was eine typische Wartung beinhaltet:
• Inspektion: Zunächst führen wir eine gründliche Inspektion des gesamten Hydrauliksystems durch. Dies umfasst die Überprüfung von Hydraulikschläuchen, -pumpen, -ventilen und -zylindern auf Zeichen von Verschleiß oder Schaden.
• Reinigung: Wir reinigen das gesamte System, um sicherzustellen, dass es frei von Verunreinigungen und Ablagerungen ist, die die Leistung beeinträchtigen könnten.
• Flüssigkeitsmanagement: Wir überprüfen das Hydrauliköl auf Klarheit, Sauberkeit und richtigen Stand. Bei Bedarf wechseln wir das Öl und die Filter, um sicherzustellen, dass Ihr System mit sauberem, frischem Öl läuft.
• Dichtungsprüfung: Wir überprüfen alle Dichtungen und O-Ringe in Ihrem System auf Verschleiß oder Schäden und tauschen diese bei Bedarf aus.
• Druck- und Temperaturüberprüfung: Wir prüfen, ob Ihr System den richtigen Druck und die richtige Temperatur aufweist, um sicherzustellen, dass es effizient und sicher funktioniert.
• Sicherheitsüberprüfung: Wir überprüfen alle Sicherheitseinrichtungen, wie Druckbegrenzungsventile, um sicherzustellen, dass sie richtig funktionieren.
• Fehlerbehebung und Reparatur: Wenn wir während der Inspektion Probleme entdecken, werden wir diese beheben oder notwendige Reparaturen durchführen, um sicherzustellen, dass Ihr Hydrauliksystem in optimalem Zustand ist.
• Beratung und Empfehlungen: Nach Abschluss der Wartung werden wir Ihnen einen ausführlichen Bericht über den Zustand Ihrer Hydraulikanlage geben und gegebenenfalls Empfehlungen für weitere Maßnahmen oder Verbesserungen geben.
Die Dauer der Wartung einer Hydraulikanlage kann stark variieren und hängt von einer Vielzahl von Faktoren ab. Dazu gehören die Größe und Komplexität der Anlage, der allgemeine Zustand der Ausrüstung, die spezifischen Wartungsaufgaben, die durchgeführt werden müssen, und ob während der Inspektion Probleme entdeckt werden, die eine zusätzliche Reparatur oder den Austausch von Komponenten erfordern.
Eine routinemäßige Wartung und Inspektion einer durchschnittlichen Hydraulikanlage kann einige Stunden in Anspruch nehmen, während eine umfangreiche Wartung, die den Austausch von Komponenten oder die Behebung komplexer Probleme erfordert, einen ganzen Tag oder länger dauern kann.
Bei HANSA-FLEX legen wir Wert darauf, Ihre Ausfallzeiten so gering wie möglich zu halten. Unsere erfahrenen Techniker arbeiten effizient, ohne Kompromisse bei der Qualität oder Sicherheit einzugehen. Wir koordinieren auch die Wartungsarbeiten nach Möglichkeit mit Ihren Betriebszeiten, um Störungen zu minimieren.
Regelmäßige Hydraulikservices sind ein entscheidender Aspekt, um die Lebensdauer und Effizienz Ihrer Hydraulikausrüstung zu maximieren. Hier sind einige Wege, wie sie dazu beitragen:
• Frühzeitige Problemidentifikation: Durch routinemäßige Inspektionen können mögliche Probleme frühzeitig erkannt und behoben werden, bevor sie zu kostspieligen Ausfällen oder Schäden führen.
• Wartung der Flüssigkeitsqualität: Die Kontrolle und Aufrechterhaltung der Hydraulikflüssigkeit in optimalem Zustand ist entscheidend, um den Verschleiß der Komponenten zu minimieren und die Leistung des Systems zu maximieren.
• Verschleißüberwachung: Regelmäßige Prüfungen ermöglichen die frühzeitige Erkennung von Verschleißerscheinungen an Komponenten und ermöglichen rechtzeitige Reparaturen oder Ersatzteile.
• Optimale Einstellung: Bei routinemäßigen Wartungen stellen wir sicher, dass alle Einstellungen, wie Druck und Temperatur, optimal sind, was zu einer verbesserten Effizienz und verlängerten Lebensdauer der Ausrüstung führt.
• Reinigung: Die regelmäßige Reinigung der Hydrauliksysteme hilft, Ablagerungen und Verunreinigungen zu entfernen, die die Leistung beeinträchtigen und den Verschleiß beschleunigen können.
• Sicherheit: Wartungsdienstleistungen umfassen auch die Überprüfung und Wartung der Sicherheitssysteme, um sicherzustellen, dass Ihre Anlagen sicher betrieben werden können.
Bei HANSA-FLEX verstehen wir, dass unerwartete Ausfälle Ihrer Hydraulikanlage nicht nur frustrierend, sondern auch kostspielig sein können. Deshalb haben wir uns dazu verpflichtet, Ihnen auch in Notfällen zur Seite zu stehen.
Wir bieten einen 24/7 Notdienst an, der darauf ausgelegt ist, Ihnen schnell und effizient zu helfen, wenn Sie ihn am meisten brauchen. Egal, ob es sich um eine kleine Reparatur oder um einen umfangreichen Ausfall handelt, unser Notdienstteam steht bereit, um schnellstmöglich vor Ort zu sein und die notwendigen Reparaturen durchzuführen.
Unsere erfahrenen Techniker sind in der Lage, eine Vielzahl von Problemen zu diagnostizieren und zu beheben, um Ihre Anlage wieder in Betrieb zu nehmen und Ausfallzeiten zu minimieren. Dabei nutzen wir modernste Diagnosetechniken und Ersatzteile von höchster Qualität, um sicherzustellen, dass Ihre Anlage nach einem Ausfall schnell und effizient wieder funktioniert.
Wir empfehlen Ihnen, unsere Notdienstnummer griffbereit zu halten, damit Sie im Falle eines unerwarteten Ausfalls schnell reagieren können. Denken Sie daran, dass die schnelle Behebung von Problemen dazu beitragen kann, die Ausfallzeiten zu minimieren und potenziell größere Schäden an Ihrer Hydraulikanlage zu vermeiden.
Bei HANSA-FLEX setzen wir uns für höchste Qualität und Kundenzufriedenheit ein. Unser Engagement für Qualität zeigt sich in unserer Arbeitsweise und den Standards, die wir erfüllen.
Um die Qualität unserer Arbeit zu sichern, verfolgen wir eine Reihe von Strategien:
• Hochqualifiziertes Personal: Unsere Techniker sind gründlich ausgebildet und verfügen über die notwendigen Zertifizierungen und Qualifikationen. Sie nehmen regelmäßig an Weiterbildungen teil, um auf dem neuesten Stand der Technik zu bleiben und unsere Kunden bestmöglich zu unterstützen.
• Qualitätsmanagement: Wir haben ein umfassendes Qualitätsmanagementsystem implementiert, das auf den Standards ISO 9001 basiert. Dieses System beinhaltet strenge Prozesse und Verfahren zur Überwachung und Verbesserung der Qualität unserer Arbeit.
• Qualitätsprüfungen: Alle unsere Produkte und Dienstleistungen unterliegen strengen Qualitätsprüfungen, um sicherzustellen, dass sie unsere hohen Standards erfüllen. Dies beinhaltet sowohl die Überprüfung der von uns verwendeten Materialien und Komponenten, als auch die Überprüfung der Qualität unserer Arbeit.
• Feedback der Kunden: Wir ermutigen unsere Kunden, uns ihr Feedback zu geben, und wir nutzen dieses Feedback, um unsere Prozesse ständig zu verbessern und noch besser auf die Bedürfnisse unserer Kunden einzugehen.
• Zertifizierungen: Wir sind nach mehreren Industriestandards zertifiziert, die unser Engagement für Qualität, Sicherheit und Umweltschutz belegen.
Unser Servicepersonal bei HANSA-FLEX repräsentiert das Herzstück unserer Unternehmensmission: die Bereitstellung herausragender Hydrauliklösungen durch technische Expertise und engagierten Kundenservice.
Zum Erreichen dieses Ziels setzen wir auf ein Team, das sich durch umfangreiche Ausbildung und weitreichende Erfahrung auszeichnet. Hier sind einige Schlüsselmerkmale:
• Umfassende Ausbildung: Jeder unserer Servicetechniker durchläuft eine umfangreiche Ausbildung, die sowohl die theoretischen Grundlagen der Hydraulik umfasst als auch praktisches Wissen zur Installation, Wartung und Reparatur hydraulischer Systeme vermittelt. Die Ausbildung schließt auch spezialisierte Themen ein, wie beispielsweise Arbeitssicherheit, Diagnosetechniken und Kundenservice.
• Stetige Weiterbildung: In einer sich schnell verändernden Branche ist kontinuierliche Weiterbildung unerlässlich. Unser Personal nimmt daher regelmäßig an Weiterbildungsmaßnahmen teil, um stets auf dem neuesten Stand der Technik zu bleiben.
• Erfahrung: Neben der Ausbildung ist praktische Erfahrung ein wesentlicher Bestandteil der Kompetenz unseres Personals. Unser Team besteht aus erfahrenen Fachleuten, die eine Vielzahl von hydraulischen Systemen und Anwendungsfällen kennen.
• Zertifizierungen: Viele unserer Techniker haben branchenspezifische Zertifizierungen, die ihre Fähigkeiten und ihr Wissen bestätigen.
• Kundenorientierung: Neben der technischen Expertise legen wir großen Wert auf hervorragenden Kundenservice. Unser Personal ist darin geschult, auf die speziellen Bedürfnisse unserer Kunden einzugehen und Lösungen zu liefern, die ihren Anforderungen entsprechen.
Bei HANSA-FLEX nehmen wir die Sicherheit bei der Wartung von Hydraulikanlagen sehr ernst. Wir verstehen, dass eine ordnungsgemäße Wartung nicht nur die Langlebigkeit und Leistung Ihrer Hydraulikanlage verbessert, sondern auch dazu beiträgt, Unfälle und Verletzungen zu vermeiden. Hier sind einige der Sicherheitsmaßnahmen, die wir ergreifen:
• Sicherheitsausrüstung: Unser Servicepersonal ist mit der notwendigen persönlichen Schutzausrüstung (PSA) ausgestattet, einschließlich Schutzhelmen, Sicherheitsbrillen, Handschuhen und geeigneten Schuhen. Darüber hinaus verwenden wir Werkzeuge und Ausrüstung, die speziell dafür konzipiert sind, die Sicherheit bei der Arbeit an Hydraulikanlagen zu gewährleisten.
• Sicherheitsschulungen: Alle unsere Servicetechniker durchlaufen umfangreiche Sicherheitsschulungen. Sie lernen die potenziellen Gefahren bei der Arbeit an Hydraulikanlagen kennen und wie sie diese vermeiden können.
• Einhalten von Sicherheitsstandards: Wir halten uns streng an alle geltenden Industriestandards und Vorschriften für Sicherheit und Gesundheitsschutz am Arbeitsplatz. Dies beinhaltet sowohl allgemeine Arbeitssicherheitsstandards als auch spezifische Vorschriften für die Arbeit an Hydraulikanlagen.
• Risikobewertung: Vor Beginn der Wartungsarbeiten führen wir eine Risikobewertung durch, um potenzielle Gefahren zu identifizieren und geeignete Sicherheitsmaßnahmen zu treffen.
• Sicherheitsprotokolle und -verfahren: Wir haben klare Sicherheitsprotokolle und -verfahren implementiert, die in allen Phasen der Wartungsarbeit befolgt werden. Dies hilft, das Risiko von Unfällen und Verletzungen zu minimieren.
Bei HANSA-FLEX sind wir stolz auf die Qualität und Zuverlässigkeit unserer Hydraulikservices. Seit vielen Jahren haben wir eine Vielzahl von Kunden in den unterschiedlichsten Branchen betreut und konnten so eine breite Palette von Projekten erfolgreich umsetzen.
Obwohl ich Ihnen aus datenschutzrechtlichen Gründen keine spezifischen Referenzen oder Kundeninformationen geben kann, können wir sicherlich einige allgemeine Beispiele für Arbeiten nennen, die wir in der Vergangenheit durchgeführt haben:
• Industrielle Anwendungen: Wir haben regelmäßig Wartungs- und Reparaturarbeiten für industrielle Hydraulikanlagen durchgeführt, von Fertigungslinien bis hin zu Verpackungssystemen.
• Bauwesen: In der Baubranche haben wir umfangreiche Erfahrungen mit der Wartung und Reparatur von Hydraulikanlagen in schweren Baumaschinen, wie Baggern, Kränen und Betonpumpen.
• Landwirtschaft: Im landwirtschaftlichen Sektor haben wir an einer Vielzahl von Hydraulikanlagen gearbeitet, darunter Traktoren, Mähdrescher und Bewässerungssysteme.
• Maritime Anwendungen: Im maritimen Bereich haben wir an Hydraulikanlagen von Schiffen und Hafenausrüstung gearbeitet.
• Mobile Hydraulik: Wir haben auch eine umfangreiche Erfahrung mit mobilen Hydrauliksystemen, wie sie in Flurförderzeugen, Nutzfahrzeugen und mobilen Arbeitsmaschinen zu finden sind. Können Sie kundenspezifische Wartungsverträge oder -pläne anbieten, die auf meine spezifischen Bedürfnisse zugeschnitten sind?
Bei HANSA-FLEX verstehen wir, dass jede Hydraulikanlage und jeder Betrieb einzigartig ist. Daher bieten wir kundenspezifische Wartungsverträge und -pläne an, die genau auf Ihre spezifischen Bedürfnisse zugeschnitten sind. Unser Ziel ist es, eine Partnerschaft mit unseren Kunden aufzubauen, die auf Vertrauen, Flexibilität und hoher Servicequalität basiert.
Unser Prozess beginnt damit, dass wir Ihre spezifischen Bedürfnisse und Anforderungen sorgfältig verstehen und bewerten. Wir berücksichtigen Faktoren wie die Art der Hydraulikanlage, die Betriebsbedingungen, die Nutzungshäufigkeit, die Anforderungen an die Betriebszeit und viele andere Parameter.
Basierend auf dieser Bewertung erstellen wir einen maßgeschneiderten Wartungsplan, der spezifische Wartungsaktivitäten, Prüfintervalle, prognostizierte Ersatzteilanforderungen und andere relevante Details enthält.
Diese kundenspezifischen Wartungspläne bieten zahlreiche Vorteile:
• Optimierung der Betriebszeit: Durch die Planung der Wartung auf der Grundlage Ihrer spezifischen Anforderungen können wir Ausfallzeiten minimieren und sicherstellen, dass Ihre Hydraulikanlage stets optimal läuft. • Kostenkontrolle: Mit einem maßgeschneiderten Wartungsvertrag können Sie Ihre Wartungskosten besser vorhersehen und kontrollieren.
• Verlängerung der Lebensdauer Ihrer Anlage: Durch regelmäßige, speziell auf Ihre Anlage abgestimmte Wartung können Sie die Lebensdauer Ihrer Hydraulikanlage verlängern und kostspielige vorzeitige Ausfälle vermeiden.
• Priorisierter Service: Kunden mit Wartungsverträgen genießen oft priorisierten Service, einschließlich bevorzugter Terminvergabe und schnellerer Reaktionszeiten.
Hydraulikdichtung
Hydraulikdichtungen sind essentiell, um das Austreten von Hydraulikflüssigkeit zu verhindern und den Druck im System aufrechtzuerhalten. Sie tragen zur Effizienz und Sicherheit des Systems bei, indem sie die Reibung minimieren und die Lebensdauer der Hydraulikkomponenten verlängern.
Es gibt verschiedene Arten von Hydraulikdichtungen, die je nach Anwendung und Druckniveau eingesetzt werden. Zu den gängigsten gehören Stangendichtungen, Kolbendichtungen, Abstreifer und O-Ringe.
Die Auswahl der richtigen Hydraulikdichtung hängt von vielen Faktoren ab, wie z.B. dem Druck im System, der Temperatur, der Bewegungsgeschwindigkeit und der Hydraulikflüssigkeit. Materialkompatibilität und die Größe der Dichtung sind entscheidend für die optimale Funktion und Langlebigkeit.
Häufige Probleme bei Hydraulikdichtungen sind Verschleiß, Verhärtung, Rissbildung und Extrusion. Diese Probleme können durch Überdruck, falsche Montage oder die Verwendung unangemessener Materialien entstehen.
Die Wartung von Hydraulikdichtungen umfasst die regelmäßige Überprüfung auf Verschleiß und Schäden, das Ersetzen von abgenutzten Dichtungen und das Halten der Hydraulikflüssigkeit sauber. Es ist wichtig, die Dichtungen mit den spezifizierten Flüssigkeiten zu verwenden, um chemische Unverträglichkeiten zu vermeiden.
Hydrauliköl
Hydrauliköl dient als Übertragungsmedium für Energie und Informationen im hydraulischen System. Es schmiert die beweglichen Teile, überträgt Kräfte, dämpft Stöße und trägt zur Kühlung der Komponenten bei.
Die Auswahl des richtigen Hydrauliköls hängt von der Art des Systems, den Betriebsbedingungen, der erforderlichen Viskosität und den Herstellervorgaben ab. Es ist wichtig, auf die Spezifikationen und Empfehlungen der Gerätehersteller zu achten, um die Kompatibilität und Leistungsfähigkeit sicherzustellen.
Die Wechselfrequenz des Hydrauliköls variiert je nach Betriebsbedingungen, Ölqualität und Herstellervorgaben. Eine regelmäßige Analyse des Ölzustands kann helfen, den optimalen Zeitpunkt für einen Wechsel zu bestimmen.
Anzeichen für kontaminiertes Hydrauliköl sind Verfärbung, Trübung, Ablagerungen oder eine Veränderung der Viskosität. Auch das Vorhandensein von Wasser oder metallischen Partikeln kann auf Kontamination hinweisen.
Das Mischen unterschiedlicher Hydrauliköle sollte vermieden werden, da es zu einer Verminderung der Schmierfähigkeit, chemischen Reaktionen oder einer Änderung der Viskosität führen kann, was die Systemleistung und Zuverlässigkeit beeinträchtigen könnte.
Hydraulikzylinder
Ein Hydraulikzylinder ist ein elementares Bauteil in hydraulischen Systemen, das dazu dient, hydraulische Energie in lineare Bewegung oder Kraft umzusetzen. Er besteht aus einem Zylindergehäuse und einem beweglichen Kolben. Der unter Druck stehende Hydraulikflüssigkeitseinlass bewirkt, dass der Kolben sich entlang der Zylinderachse bewegt, wodurch eine lineare Kraft ausgeübt wird.
Die Unterschiede zwischen den Hydraulikzylindertypen liegen in ihrer Bauform und Funktion. Einfachwirkende Zylinder erzeugen eine Kraft in nur einer Richtung, während doppeltwirkende Zylinder in beide Richtungen Kräfte ausüben können. Teleskopzylinder bieten eine längere Hublänge und werden oft in Anwendungen wie Kipplastwagen verwendet.
Für die Herstellung von Hydraulikzylindern werden Materialien wie Stahl, Edelstahl oder Aluminium verwendet, die aufgrund ihrer mechanischen Eigenschaften und Korrosionsbeständigkeit ausgewählt werden. Die Dichtungen sind in der Regel aus synthetischen Gummiarten, um eine dauerhafte Abdichtung zu gewährleisten.
Die Dimensionierung eines Hydraulikzylinders hängt von den Anforderungen der Anwendung ab. Wichtige Faktoren sind die zu erzeugende Kraft, die Hublänge und die Arbeitsgeschwindigkeit. Die Zylindergröße wird durch den erforderlichen Druck und die Flächen des Kolbens bestimmt, wobei die Kolbenfläche die auf den Kolben wirkende Kraft bestimmt.
Die Lebensdauer eines Hydraulikzylinders kann durch regelmäßige Wartung, sachgerechte Nutzung und Schutz vor Überlastung verlängert werden. Wichtig ist auch, dass die verwendete Hydraulikflüssigkeit sauber ist und die Zylinderdichtungen intakt sind, um Leckagen und Verunreinigungen zu vermeiden.
Hydraulikpresse
Eine Hydraulikpresse ist eine Maschine, die mithilfe hydraulischer Zylinder Druck ausübt, um Materialien zu formen, zu pressen oder zu stanzen. Sie wird in der Fertigungsindustrie eingesetzt, um Teile mit hoher Präzision zu bearbeiten oder zu verbinden, wie etwa beim Tiefziehen, Prägen oder Zusammenfügen von Metallteilen.
Die Auswahl der richtigen Hydraulikpresse hängt von der zu erledigenden Aufgabe ab. Wichtige Faktoren sind die erforderliche Presskraft, die Größe der Werkstücke, die Geschwindigkeit, mit der die Presse arbeiten soll, und spezielle Funktionen, die für bestimmte Prozesse benötigt werden, wie beispielsweise einstellbare Pressgeschwindigkeit oder Heizplatten.
Zu den Sicherheitsvorkehrungen beim Betrieb einer Hydraulikpresse gehören der Einsatz von Schutzgittern oder Lichtschranken, um den Bediener zu schützen, regelmäßige Inspektionen und Wartungen der Presse, das Tragen von persönlicher Schutzausrüstung und die Schulung der Bediener in den korrekten Betriebsverfahren.
Die Wartung einer Hydraulikpresse umfasst die Überprüfung von Hydrauliköl und -filtern, das Nachziehen von Schraubverbindungen, die Inspektion von Dichtungen und Schläuchen auf Verschleiß und Leckagen, sowie die Überprüfung der Sicherheitseinrichtungen. Eine regelmäßige Wartung ist entscheidend, um die Zuverlässigkeit und Sicherheit der Presse zu gewährleisten.
Die Effizienz einer Hydraulikpresse kann verbessert werden, indem man sicherstellt, dass alle Komponenten ordnungsgemäß gewartet und eingestellt sind, dass das Hydrauliksystem sauber gehalten wird, und dass die Presse korrekt für die spezifischen Aufgaben konfiguriert ist. Optimierungen des Prozesses und der Werkzeuge können ebenfalls zu Effizienzsteigerungen führen.
Pneumatik
Pneumatik ist die Technik, die Druckluft zur Energieübertragung nutzt. Sie wandelt Druckenergie in mechanische Arbeit um, meist für Bewegungs- und Positionieraufgaben. Das Pneumatiksystem umfasst Komponenten wie Kompressoren, Ventile, Zylinder und Sensoren, die zusammenarbeiten, um Luft zu komprimieren, zu steuern und Bewegungen zu erzeugen.
Pneumatiksysteme sind in der Regel einfacher und sauberer als Hydrauliksysteme, da sie Luft statt Öl verwenden. Sie sind oft schneller, leichter und bieten eine sichere Lösung in explosionsgefährdeten Bereichen. Außerdem sind Pneumatikkomponenten meist kostengünstiger und wartungsärmer.
Pneumatik findet in vielfältigen Bereichen Anwendung, darunter in der Automatisierungstechnik, in der Robotik und in der Medizintechnik, insbesondere dort, wo eine saubere Umgebung erforderlich ist oder schnelle, wiederholbare Bewegungen gefordert sind.
Die Wartung pneumatischer Systeme umfasst regelmäßige Kontrollen auf Leckagen, das Überprüfen und Ersetzen von Filtern und Trocknern, das Überwachen der Luftqualität und das Prüfen der Schlauchverbindungen. Eine adäquate Wartung sichert eine zuverlässige Funktion und verlängert die Lebensdauer der Komponenten.
Zu den Pneumatikkomponenten zählen Zylinder, die lineare Bewegungen ausführen, Ventile, die den Luftstrom steuern, Druckregler, die den Druck in einem System regeln, sowie Schläuche und Verbindungen, die die Luft zu den verschiedenen Komponenten des Systems führen.
Pneumatikschlauch
Pneumatikschläuche sind flexibel, beständig gegenüber Abnutzung und müssen den spezifischen Druckanforderungen der pneumatischen Systeme standhalten. Sie sind in verschiedenen Materialien und Größen für unterschiedliche Anwendungen und Umgebungsbedingungen erhältlich.
Beim Auswählen des richtigen Pneumatikschlauches müssen der Betriebsdruck, die Temperatur, die chemische Beständigkeit und der Biegeradius berücksichtigt werden. Die Schlauchdimensionierung muss den Volumenstromanforderungen des Systems entsprechen, um eine effiziente Leistung sicherzustellen.
Die korrekte Installation eines Pneumatikschlauches erfordert die Beachtung des richtigen Biegeradius, das Vermeiden von Quetschungen und das Sichern der Schlauchenden mit passenden Anschlüssen und Klemmen, um Leckagen zu verhindern.
Häufige Fehler bei der Verwendung von Pneumatikschläuchen sind unsachgemäße Installation, die zu Leckagen führt, die Verwendung von Schläuchen außerhalb ihrer Spezifikationen, was zu vorzeitigem Versagen führen kann, und unzureichende Wartung, die die Lebensdauer verkürzt.
Drucktests bei Pneumatikschläuchen sollten in Übereinstimmung mit den Sicherheitsvorschriften durchgeführt werden, indem der Schlauch in einer kontrollierten Umgebung auf den maximalen Betriebsdruck aufgebracht wird, um auf Dichtigkeit und Festigkeit zu überprüfen.
Pneumatikzylinder
Pneumatikzylinder nutzen komprimierte Luft, um Bewegungen zu erzeugen, während Hydraulikzylinder durch Flüssigkeiten angetrieben werden. Dies macht Pneumatikzylinder ideal für Anwendungen, die Sauberkeit erfordern oder wo keine Flüssigkeitsleckage toleriert werden kann.
Pneumatikzylinder werden häufig in industriellen Automatisierungsprozessen eingesetzt, wo leichte bis mittelschwere Lasten bewegt werden müssen. Sie sind auch in der Verpackungsindustrie und in Anwendungen, wo schnelle oder präzise Bewegungen erforderlich sind, weit verbreitet.
Die Kraft eines Pneumatikzylinders wird durch das Produkt aus dem Druck der Luft und der Fläche des Kolbens berechnet. Die Kolbenfläche ist dabei die Oberfläche, auf die der Druck wirkt, um die Bewegung zu erzeugen.
Zu den wichtigsten Wartungsmaßnahmen gehören das Überprüfen auf Abnutzung und Beschädigungen, das Ersetzen von Dichtungen und Kolbenringen sowie das Sicherstellen, dass keine Fremdkörper die Bewegung des Zylinders stören.
Probleme bei Pneumatikzylindern können durch Überprüfung der Luftversorgung, das Hören auf ungewöhnliche Geräusche, das Suchen nach Leckagen und das Prüfen der Bewegung auf Ruckeln oder Abweichungen diagnostiziert werden.
Adapter
Hydraulikadapter sind Komponenten, die in Hydrauliksystemen verwendet werden, um unterschiedliche Gewinde- oder Anschlussarten miteinander zu verbinden. Sie gewährleisten die Kompatibilität zwischen verschiedenen Teilen des Systems und ermöglichen so eine flexible und sichere Verbindung.
Es gibt verschiedene Typen von Hydraulikadaptern, darunter:
• Gewindeadapter: Verbindet Gewinde unterschiedlicher Art.
• Übergangsadapter: Wandelt eine Anschlussart in eine andere um.
• Winkeladapter: Ändert die Richtung des Flusses innerhalb des Systems.
• T-Stück-Adapter: Erlaubt den Anschluss eines dritten Elements an eine bestehende Leitung.
Die Wahl des richtigen Adapters hängt von verschiedenen Faktoren ab:
• Anschlussart und Gewinde: Der Adapter muss zu den Gewinden und Anschlüssen des bestehenden Systems passen.
• Druckanforderungen: Der Adapter muss für den maximalen Druck des Systems geeignet sein.
• Material: Das Material des Adapters sollte kompatibel mit dem Medium im System sein (z.B. korrosionsbeständige Materialien für aggressive Medien).
Während Adapter in erster Linie dazu dienen, verschiedene Gewinde- oder Anschlussarten zu verbinden und die Kompatibilität zu gewährleisten, sind Armaturen spezifische Komponenten, die für das Ein- und Ausschalten des Flusses oder für Druck- und Flussregelung verwendet werden. Armaturen übernehmen oft spezifischere Funktionen in Hydrauliksystemen.
Wichtige Normen für Hydraulikadapter umfassen:
• ISO 8434: Standards für 37° JIC- und 90° ORFS-Anschlüsse.
• DIN 2353: Standards für metrische Verschraubungen.
• SAE J514: Standards für Rohrverschraubungen in Hydrauliksystemen.
Hydraulikadapter bieten folgende Vorteile:
• Flexibilität: Sie ermöglichen die Verbindung unterschiedlicher Systemkomponenten.
• Einfache Integration: Adapter erleichtern die Nachrüstung und Erweiterung bestehender Systeme.
• Sicherer Betrieb: Sie tragen zur Aufrechterhaltung der Dichtheit und Integrität des Systems bei.
Bei der Installation von Hydraulikadaptern sind folgende Schritte zu beachten:
• Überprüfen der Kompatibilität: Sicherstellen, dass der Adapter zu den Gewinden und Anschlüssen passt.
• Verwenden von Dichtmitteln: Dichtmittel sollten entsprechend der Spezifikation für die Verbindung genutzt werden.
• Drehmoment beachten: Den Adapter gemäß den Vorgaben des Herstellers anziehen, um Über- oder Unterdrehungen zu vermeiden.
Flansche
Ein Flansch ist ein ringförmiges Bauteil, das an den Enden von Rohren, Schläuchen oder Behältern montiert wird. Flansche ermöglichen die Verbindung und Abdichtung von Rohrleitungen, Geräten oder Maschinen. Sie dienen zur Erleichterung von Montage und Demontage und bieten eine Möglichkeit zur Wartung oder Erweiterung des Systems.
- Losflansch: Kann sich unabhängig vom Rohr drehen, erleichtert die Ausrichtung.
- Blindflansch: Dient zum Verschließen des Rohrendes.
- Gewindeflansch: Verfügt über ein Innengewinde, das auf ein Außengewinde des Rohrs geschraubt wird.
- Schweißflansch: Wird durch Schweißen fest mit dem Rohr verbunden.
- Aufschweißflansch: Ermöglicht Schweißen an der Rohrleitung und bietet eine zusätzliche Dichtfläche.
Flansche werden aus verschiedenen Materialien hergestellt, abhängig von den Anforderungen der Anwendung:
- Edelstahl: Korrosionsbeständig und für hohe Temperaturen geeignet.
- Kohlenstoffstahl: Bietet hohe Festigkeit und ist wirtschaftlich für allgemeine Anwendungen.
- Kunststoffe: Für leichtere, korrosionsfreie Anwendungen.
- Kupfer: Wird oft in Vakuumsystemen verwendet, besonders in CF-Flanschen.
Flansche werden üblicherweise mit Dichtungen versehen, um eine leckfreie Verbindung zu gewährleisten. Die Dichtungen können aus Gummi, PTFE, Metall oder anderen Materialien bestehen, je nach den Anforderungen des Systems wie Druck, Temperatur und Medium.
Flansche werden in vielen Bereichen eingesetzt:
- Industrie: Verbindung von Rohrleitungen für Prozessanlagen.
- Heizungstechnik: Dichtung und Verbindung von Heizungsrohren.
- Vakuumtechnik: CF-Flansche für ultrahochvakuum Anwendungen.
- Anlagenbau: Für Druckbehälter und Rohrleitungssysteme.
CF-Flansche (ConFlat) verwenden eine metallische Dichtung, oft aus Kupfer, und sind speziell für Ultrahochvakuum (UHV) Anwendungen konzipiert. Sie können hohen Temperaturen standhalten und bieten eine extrem dichte Verbindung, die bei anderen Flanschtypen nicht immer gewährleistet ist.
Installation:
- Ausrichtung: Flansche müssen korrekt ausgerichtet und angezogen werden.
- Dichtung: Dichtungen müssen sauber und korrekt positioniert sein.
- Drehmoment: Bolzen sollten gleichmäßig und in der richtigen Reihenfolge angezogen werden.
Wartung:
- Inspektion: Regelmäßige Überprüfung auf Leckagen und Beschädigungen.
- Erneuerung: Bei Abnutzung oder Leckagen Dichtungen und Bolzen ersetzen.
Formschläuche
Formschläuche sind speziell geformte Schläuche, die in Anwendungen eingesetzt werden, in denen herkömmliche, gerade Schläuche nicht praktikabel sind. Sie werden meist verwendet, wenn komplexe Biegungen und bestimmte räumliche Anforderungen vorliegen, wie z.B. in Motorenräumen von Fahrzeugen.
Formschläuche können aus verschiedenen Materialien wie Silikon, EPDM (Ethylen-Propylen-Dien-Kautschuk), NBR (Nitrilkautschuk), und anderen Gummimischungen hergestellt werden. Die Materialwahl hängt von den Anforderungen an Temperaturbeständigkeit, Chemikalienresistenz und Flexibilität ab.
Formschläuche werden meist durch Formpressen hergestellt. Dabei wird das Material in eine Form gepresst und bei hohen Temperaturen vulkanisiert. Dies ermöglicht die Herstellung von Schläuchen in spezifischen Formen und Größen.
Formschläuche finden Anwendung in vielen Bereichen, darunter Fahrzeugbau, Maschinenbau, Medizintechnik und Haushaltsgeräte. Sie sind besonders nützlich in Umgebungen, in denen Platz begrenzt ist oder genaue Biegungen erforderlich sind.
Formschläuche bieten eine präzise Passform und ermöglichen die optimale Raumnutzung in komplexen Umgebungen. Sie minimieren das Risiko von Knicken und verbessern die Leistung und Lebensdauer von Systemen durch ihre angepasste Form.
Formschläuche werden normalerweise fertig geformt geliefert, um die genauen Spezifikationen zu erfüllen. Ein nachträgliches Biegen oder Formen ist nicht empfehlenswert, da dies die Struktur und Funktionalität des Schlauchs beeinträchtigen kann.
Bei der Auswahl eines Formschlauchs sollte man die spezifischen Anforderungen der Anwendung berücksichtigen, einschließlich des Durchmessers, der Form, der Materialbeständigkeit und der Temperaturanforderungen. Es ist auch wichtig sicherzustellen, dass der Schlauch den Druckanforderungen der Anwendung standhält.
Formschläuche sollten an einem kühlen, trockenen Ort gelagert werden, geschützt vor direktem Sonnenlicht und Ozon. Sie sollten nicht in engem Biegeradius oder unter mechanischer Belastung gelagert werden, um Verformungen zu vermeiden.
Industrieschläuche
Industrieschläuche sind spezielle Schläuche, die in einer Vielzahl von industriellen Anwendungen eingesetzt werden, um Flüssigkeiten, Gase oder Feststoffe zu transportieren. Sie finden Verwendung in Bereichen wie der Chemie-, Lebensmittel-, Bau- und Landwirtschaftsindustrie.
Industrieschläuche können aus verschiedenen Materialien hergestellt werden, darunter PVC, Polyurethan (PU), Gummi, Edelstahl, und Teflon. Die Materialwahl hängt von den spezifischen Anforderungen wie chemische Beständigkeit, Temperatur und Druck ab.
Zu den häufigsten Typen gehören Wasser-, Luft- und Gasschläuche, Schläuche für Öle und Kraftstoffe, Feststoffschläuche, sowie Schläuche für Chemikalien und Lebensmittel. Jede Art ist für bestimmte Einsatzbereiche optimiert.
Die Wahl des richtigen Schlauches sollte auf den Anforderungen der Anwendung basieren, wie Druck, Temperatur, Medium, das transportiert wird, und der benötigten Flexibilität. Schläuche sollten auch den jeweiligen Normen und Vorschriften entsprechen.
Die Lebensdauer wird beeinflusst durch Betriebsbedingungen wie Druck, Temperatur, Abrieb, UV-Licht, chemische Einflüsse und den Biegeradius. Regelmäßige Inspektionen und korrekte Lagerung können die Lebensdauer verlängern.
Industrieschläuche sollten regelmäßig auf Risse, Abrieb, und Undichtigkeiten überprüft werden. Zudem sollte man darauf achten, dass sie nicht übermäßig geknickt oder gedehnt werden. Schläuche sollten trocken und sauber gelagert werden, um die Materialbeständigkeit zu erhalten.
Industrieschläuche müssen je nach Anwendung unterschiedlichen Normen entsprechen, wie z.B. ISO, DIN, und ASTM-Standards, die Anforderungen an Druck, Temperatur und Beständigkeit regeln.
Schläuche sollten trocken, kühl und fern von direkter Sonneneinstrahlung gelagert werden. Sie sollten nicht in engen Biegeradien gelagert werden, um Materialermüdung zu vermeiden.
Kompensatoren
Kompensatoren sind flexible Elemente in Rohrleitungen, die Bewegungen, Vibrationen und thermische Ausdehnungen aufnehmen. Sie schützen die Rohrleitungen und verbundenen Komponenten vor Belastungen, die durch Druck, Temperaturänderungen oder mechanische Kräfte entstehen.
Die Haupttypen von Kompensatoren sind:
- Gummikompensatoren: Flexibel und korrosionsbeständig, ideal für Systeme mit Bewegungen und Vibrationen.
- Stahlkompensatoren: Robuste Lösung für hohe Temperaturen und Drücke.
- PTFE-Kompensatoren: Beständig gegen chemische Angriffe und hohe Temperaturen, gut geeignet für aggressive Medien
Kompensatoren werden eingesetzt, um:
- Wärmeausdehnung: Aufnahme von Ausdehnungen bei Temperaturänderungen in Rohrleitungen.
- Vibrationen: Dämpfung von Schwingungen, die von Pumpen oder Maschinen ausgehen.
- Bewegungsausgleich: Kompensation von Bewegungen oder Setzungen in Bauwerken und Anlagen
Bei der Auswahl eines Kompensators sollten folgende Faktoren berücksichtigt werden:
- Betriebsbedingungen: Druck, Temperatur und Medium.
- Art der Bewegung: Axial, lateral oder angular.
- Materialanforderungen: Beständigkeit gegenüber dem Medium und den Umgebungsbedingungen.
- Einbausituation: Platz, Anschlussart und Bewegungsaufnahme
Für die korrekte Installation von Kompensatoren:
- Vorbereitung: Überprüfen Sie die Leitungen auf Schmutz und Fremdkörper.
- Einbau: Montieren Sie den Kompensator spannungsfrei und achten Sie auf die richtige Ausrichtung.
- Befestigung: Stellen Sie sicher, dass keine zusätzlichen Kräfte durch unsachgemäße Befestigungen wirken.
- Kontrolle: Überprüfen Sie nach der Installation die Dichtheit und Bewegungsfreiheit
Regelmäßige Wartung umfasst:
- Visuelle Inspektion: Überprüfen auf Risse, Verschleiß oder Deformationen.
- Funktionsprüfung: Sicherstellen, dass der Kompensator Bewegungen korrekt aufnimmt.
- Austausch: Gegebenenfalls rechtzeitiger Austausch bei Anzeichen von Ermüdung oder Beschädigung
Kugelhähne
Kugelhähne sind Absperrventile, die durch eine drehbare Kugel im Inneren des Ventils den Durchfluss eines Mediums steuern. Sie bestehen aus einem Gehäuse, einer Kugel mit einer Bohrung, einer Welle und Dichtungen. Durch Drehen der Kugel um 90 Grad wird der Durchfluss geöffnet oder geschlossen.
- Zwei-Wege-Kugelhähne: Regulieren den Durchfluss in einer Leitung.
- Drei-Wege-Kugelhähne: Lenken den Durchfluss zwischen zwei Ausgängen.
- Vier-Wege-Kugelhähne: Eignen sich für komplexere Schaltungen in hydraulischen Systemen.
Hydraulische Kugelhähne werden in hydraulischen Systemen zur Absperrung, Steuerung und Umleitung von Hydraulikflüssigkeiten verwendet. Sie finden Anwendung in der Industrie, im Maschinenbau und in mobilen Hydraulikanlagen wie Baumaschinen und landwirtschaftlichen Geräten.
Kugelhähne bieten zahlreiche Vorteile:
- Schnelle Bedienung: Durch einfache 90-Grad-Drehung.
- Geringer Strömungswiderstand: Dank voller Bohrung.
- Lange Lebensdauer: Robuste Konstruktion und wenig Verschleiß.
- Zuverlässigkeit: Sichere Absperrung ohne Leckagen.
Berücksichtigen Sie bei der Auswahl:
- Druckbereich: Der Kugelhahn muss für den maximalen Systemdruck geeignet sein.
- Material: Wählen Sie je nach Medium korrosionsbeständige Materialien wie Edelstahl.
- Größe und Anschluss: Die Anschlussgrößen müssen zur Leitung passen.
- Funktionsweise: Wählen Sie den passenden Typ (z.B. zwei- oder drei-Wege) je nach Anforderung.
Installation:
- Überprüfen Sie die Kompatibilität: Stellen Sie sicher, dass der Kugelhahn zur Leitung passt.
- Verwenden Sie Dichtungen: Nutzen Sie passende Dichtmittel und ziehen Sie die Verbindungen gemäß den Anweisungen des Herstellers an.
Wartung:
- Regelmäßige Inspektion: Überprüfen Sie den Kugelhahn auf Verschleiß und Dichtheit.
- Reinigung: Entfernen Sie Ablagerungen und Schmutz.
- Austausch: Ersetzen Sie defekte oder verschlissene Kugelhähne rechtzeitig.
Typische Dichtungsmaterialien sind:
- PTFE (Teflon): Beständig gegen viele Chemikalien.
- EPDM: Gute Beständigkeit gegen Heißwasser und Dampf.
- Viton: Hervorragend für hohe Temperaturen und aggressive Medien.
Kupplungen
Hydraulikkupplungen sind Komponenten, die verwendet werden, um zwei Hydraulikleitungen schnell und sicher miteinander zu verbinden oder zu trennen. Sie ermöglichen den einfachen Wechsel von Werkzeugen oder die Wartung von Hydrauliksystemen ohne großen Aufwand.
Es gibt verschiedene Arten von Hydraulikkupplungen:
- Schnellkupplungen: Erlauben eine schnelle Verbindung und Trennung.
- Schraubkupplungen: Bieten eine sichere Verbindung für hohe Drücke und starke Vibrationen.
- Plattenkupplungen: Werden verwendet, um mehrere Leitungen gleichzeitig zu verbinden und trennen.
Die Wahl der richtigen Kupplung hängt von mehreren Faktoren ab:
- Druckbereich: Die Kupplung muss für den maximalen Betriebsdruck des Systems geeignet sein.
- Durchflussrate: Die Kupplung sollte den Anforderungen an die Durchflussmenge entsprechen.
- Kompatibilität: Die Anschlussgrößen und Gewindetypen müssen zur bestehenden Hydraulik passen.
- Anwendungsbereich: Beachten Sie spezielle Anforderungen, z.B. für den Einsatz in aggressiven Umgebungen oder unter hohen Belastungen.
Schnellkupplungen funktionieren durch ein Mechanismus, der das Ein- und Auskoppeln der Leitung ermöglicht, ohne das System entleeren zu müssen. Beim Verbinden verriegelt ein federbelastetes Ventil die Kupplung, während beim Trennen automatisch ein Dichtungsmechanismus aktiviert wird, um das Austreten von Hydraulikflüssigkeit zu verhindern.
Hydraulikkupplungen bieten mehrere Vorteile:
- Zeitersparnis: Schnelles Verbinden und Trennen reduziert Ausfallzeiten.
- Flexibilität: Erlaubt den einfachen Wechsel von Anbaugeräten oder Werkzeugen.
- Sicherheit: Reduziert das Risiko von Leckagen und Kontamination.
Installation:
- Kompatibilität prüfen: Stellen Sie sicher, dass Kupplungen und Leitungen zueinander passen.
- Dichtheit sicherstellen: Verwenden Sie geeignete Dichtungsmittel und ziehen Sie die Verbindungen gemäß den Herstellervorgaben an.
Wartung:
- Regelmäßige Inspektion: Überprüfen Sie Kupplungen auf Verschleiß oder Schäden.
- Reinigung: Halten Sie die Kupplungen frei von Schmutz und Ablagerungen.
- Austausch: Ersetzen Sie defekte oder stark abgenutzte Kupplungen rechtzeitig.
Hydraulikkupplungen werden in vielen Bereichen eingesetzt:
- Landwirtschaft: Schnellwechselsysteme für Traktoren und Anbaugeräte.
- Bauindustrie: Verbindung von Hydraulikhämmern, Scheren und anderen Werkzeugen.
- Industrieanlagen: Wartung und Modifikation von Hydrauliksystemen in Maschinen und Produktionslinien.
Metallschläuche
Metallschläuche sind flexible Schläuche aus Metall, die in anspruchsvollen Anwendungen verwendet werden, wo hohe Temperaturen, Drücke oder chemische Beständigkeit gefordert sind. Sie eignen sich besonders für den Transport von Flüssigkeiten und Gasen unter extremen Bedingungen.
Es gibt hauptsächlich zwei Typen von Metallschläuchen: gewellte und gewickelte Schläuche. Gewellte Schläuche bieten bessere Flexibilität und Druckbeständigkeit, während gewickelte Schläuche für bestimmte Einsatzbereiche geeignet sind, wo weniger Flexibilität benötigt wird.
Metallschläuche bieten hervorragende Beständigkeit gegen hohe Temperaturen, Druck, und aggressive Medien. Sie sind langlebig, flexibel, und bieten hohe mechanische Festigkeit.
Metallschläuche sind ideal für Anwendungen, die hohe Temperaturen, extreme Drücke, oder eine chemische Beständigkeit erfordern, wie z.B. in der Chemieindustrie, in Kraftwerken, oder in der Luft- und Raumfahrt.
Metallschläuche werden entweder durch das Wickeln von Metallstreifen (gewickelte Schläuche) oder durch das Pressen und Schweißen von Metallrohren (gewellte Schläuche) hergestellt. Gewellte Schläuche bieten in der Regel bessere Flexibilität und Druckfestigkeit.
Die häufigsten Materialien für Metallschläuche sind Edelstahl, Kupfer, und andere korrosionsbeständige Metalle. Die Wahl des Materials hängt von der chemischen Beständigkeit und den mechanischen Anforderungen der Anwendung ab.
Metallschläuche müssen häufig internationalen Normen wie DIN, ISO, oder ASTM entsprechen, die Anforderungen an Druck, Temperatur, und Beständigkeit festlegen.
Die Auswahl eines Metallschlauchs sollte auf den spezifischen Anforderungen der Anwendung basieren, einschließlich des maximalen Drucks, der Betriebstemperatur, der chemischen Beständigkeit und der benötigten Flexibilität.
PFTE Schläuche
PTFE-Schläuche bestehen aus Polytetrafluorethylen (PTFE), einem Material, das für seine hohe Temperaturbeständigkeit und chemische Resistenz bekannt ist. Sie sind ideal für den Transport aggressiver Chemikalien und in Anwendungen, bei denen hohe Reinheit gefordert wird.
PTFE-Schläuche werden häufig in der chemischen Industrie, der Lebensmittel- und Getränkeindustrie, der Pharmazie und in der Elektronik verwendet. Ihre hohe Beständigkeit gegen Chemikalien und Temperaturen macht sie ideal für den Einsatz in anspruchsvollen Umgebungen.
- Chemische Beständigkeit: Resistent gegen fast alle Chemikalien.
- Temperaturbeständigkeit: Einsatzfähig in einem breiten Temperaturbereich von -200°C bis +260°C.
- Niedrige Reibung: Glatte Oberflächen, die Ablagerungen und Verunreinigungen minimieren.
- Reinheit: Geruchs- und geschmacksneutral, daher geeignet für Lebensmittel und pharmazeutische Anwendungen.
PTFE-Schläuche werden durch Extrusion von PTFE-Granulat hergestellt. Der Prozess kann angepasst werden, um verschiedene Durchmesser und Wandstärken zu erzeugen. Verstärkungen wie Edelstahlgeflechte können hinzugefügt werden, um die Druckfestigkeit zu erhöhen.
PTFE-Schläuche sind aufgrund ihrer glatten, nicht haftenden Oberfläche leicht zu reinigen. Sie können durch einfaches Spülen mit Wasser oder anderen Lösungsmitteln gereinigt werden, ohne dass Rückstände zurückbleiben.
Obwohl PTFE-Schläuche viele Vorteile bieten, können sie bei mechanischer Beanspruchung (wie starke Biegungen) beschädigt werden. Ihre thermische Stabilität kann bei Temperaturen über 260°C abnehmen, und sie sind in der Regel weniger flexibel als andere Kunststoffschläuche.
Ja, viele PTFE-Schläuche sind für den Kontakt mit Lebensmitteln zugelassen, da sie keine Gerüche oder Geschmäcker übertragen und leicht zu reinigen sind. Sie erfüllen häufig die Anforderungen der FDA (Food and Drug Administration).
Umformsystem
Ein Umformsystem ist ein mechanisches System, das verwendet wird, um die Form eines Materials, wie z. B. eines Metallrohrs, zu ändern. Es nutzt verschiedene Methoden wie Biegen, Drücken, Ziehen oder Rollen, um das Material in die gewünschte Form zu bringen. Diese Systeme sind essenziell in der Fertigungstechnik, um präzise Formen und Strukturen zu erzeugen.
Ein Umformsystem bietet mehrere Vorteile, darunter:
- Präzision: Ermöglicht genaue Formen und Abmessungen.
- Effizienz: Reduziert die Produktionszeit durch automatisierte Prozesse.
- Materialschonung: Minimiert Materialabfall durch präzise Kontrolle der Umformprozesse.
- Flexibilität: Kann für eine Vielzahl von Materialien und Formen eingesetzt werden
Zu den gängigen Arten von Umformsystemen gehören:
- Biegemaschinen: Für das Biegen von Rohren und Blechen.
- Ziehmaschinen: Zum Verlängern oder Verformen von Materialien durch Zugkräfte.
- Walzen: Für das Umformen durch Drücken und Rollen.
- Hydraulische Pressen: Für präzise Umformarbeiten unter hohem Druck
Umformsysteme werden in zahlreichen Branchen eingesetzt, darunter:
- Automobilindustrie: Zur Herstellung von Karosserieteilen und Auspuffsystemen.
- Bauindustrie: Für die Fertigung von Stahlträgern und Rohren.
- Luft- und Raumfahrt: Zur Produktion von Leichtbauteilen und strukturellen Komponenten.
- Medizintechnik: Zur Herstellung präziser medizinischer Geräte und Implantate
Schlauchleitungskonfigurator
Ein Schlauchleitungskonfigurator ist ein Online-Tool, das Ihnen hilft, die richtige Schlauchleitung für Ihre spezifischen Anforderungen zu finden. Sie können Parameter wie Material, Länge, Durchmesser, und Armaturen auswählen, um die ideale Schlauchleitung zu konfigurieren.
Ein Konfigurator ermöglicht eine schnelle und präzise Auswahl von Schlauchleitungen, reduziert Fehler, und spart Zeit. Zudem können individuelle Anforderungen wie spezielle Druckstufen oder Temperaturbereiche direkt berücksichtigt werden.
Sie geben die benötigten Spezifikationen ein, wie z.B. Durchmesser, Länge, Material, und Druckanforderungen. Der Konfigurator bietet dann passende Optionen und ermöglicht oft eine direkte Bestellung oder Anfrage.
Wichtige Informationen umfassen den gewünschten Schlauchtyp, Länge, Innendurchmesser, Material, Betriebsdruck, Betriebstemperatur und die benötigten Armaturen. Diese Daten sind entscheidend, um eine passende Schlauchleitung auszuwählen.
Ja, viele Konfiguratoren bieten die Möglichkeit, individuelle Anpassungen vorzunehmen, wie z.B. spezielle Druckbereiche, chemische Beständigkeiten oder besondere Anschlussarten.
Ein Konfigurator kann nicht alle extremen oder sehr speziellen Anforderungen abdecken. Bei besonders komplexen Anforderungen ist es ratsam, zusätzlich einen Fachmann zu konsultieren.
Die Angaben im Konfigurator dienen als Hilfestellung und sind in der Regel genau. Dennoch sollten die Konfigurationen vor dem finalen Kauf geprüft werden, um sicherzustellen, dass sie alle Spezifikationen und Anforderungen erfüllen.
Schlauchleitungen
Schlauchleitungen sind flexible Rohre, die zur Leitung von Flüssigkeiten oder Gasen dienen. Sie finden Anwendung in der Industrie, im Bauwesen, in Fahrzeugen und in vielen weiteren Bereichen.
Schlauchleitungen können aus Gummi, Teflon (PTFE), Metall oder thermoplastischen Kunststoffen gefertigt sein. Die Wahl des Materials hängt von den Einsatzbedingungen wie Temperatur, Druck und chemischer Beständigkeit ab.
Ein zu kleiner Biegeradius kann die Lebensdauer von Schlauchleitungen verkürzen, da es zu Materialermüdung und -beschädigung führen kann.
Zu den häufigen Problemen zählen Knicke, Risse, Lecks und Materialverschleiß. Auch eine falsche Lagerung oder Installation kann zu Problemen führen.
Die Wartungsintervalle hängen von den Betriebsbedingungen ab. Regelmäßige Inspektionen auf Verschleiß und Schäden sind jedoch wichtig, um einen sicheren Betrieb zu gewährleisten. Der Austausch sollte erfolgen, wenn sichtbare Schäden auftreten oder die vorgeschriebene Einsatzdauer erreicht ist.
Wichtige Standards umfassen DIN, ISO und SAE. Diese Normen legen Anforderungen an die Konstruktion, Leistung und Prüfung von Schlauchleitungen fest.
Schutzmaßnahmen umfassen die Verwendung von speziellen Schutzummantelungen, Feuerschutzschläuchen oder hitzebeständigen Materialien. Es ist wichtig, dass die Schlauchleitungen für die vorgesehenen Temperaturbereiche spezifiziert sind.
Bei der Auswahl sollten der Betriebsdruck, die Betriebstemperatur, die chemische Beständigkeit, der Biegeradius und die mechanische Belastung berücksichtigt werden.
Schlaucharmaturen
Schlaucharmaturen sind Verbindungselemente, die Schläuche mit anderen Komponenten wie Rohren, Ventilen oder Maschinen verbinden. Sie sind entscheidend, um sichere und dichte Verbindungen in hydraulischen und pneumatischen Systemen zu gewährleisten.
Es gibt verschiedene Arten von Schlaucharmaturen, darunter:
- Pressarmaturen: Werden durch Verpressen fest mit dem Schlauch verbunden.
- Schraubarmaturen: Schrauben sich in den Schlauch ein und bieten eine schnelle Verbindungslösung.
- Steckarmaturen: Bieten eine einfache und werkzeuglose Verbindung durch Stecken und Verriegeln.
Die Auswahl der richtigen Schlaucharmatur hängt ab von:
- Schlauchtyp: Die Armatur muss kompatibel mit dem verwendeten Schlauchmaterial sein.
- Betriebsbedingungen: Druck, Temperatur und Medium müssen berücksichtigt werden.
- Verbindungsart: Je nach Anwendung kann eine Press-, Schraub- oder Steckverbindung geeigneter sein.
Häufige Probleme sind:
- Leckagen: Durch unsachgemäße Montage oder Materialermüdung.
- Korrosion: Durch ungeeignete Materialien für das transportierte Medium.
- Verschleiß: Durch mechanische Belastungen oder aggressive Medien.
Für die korrekte Installation sollten folgende Schritte beachtet werden:
- Schlauch vorbereiten: Das Schlauchende muss sauber und glatt geschnitten sein.
- Armatur montieren: Die Armatur muss gemäß den Anweisungen des Herstellers montiert werden.
- Dichtheit prüfen: Nach der Montage sollte das System auf Dichtheit geprüft werden.
Schlaucharmaturen unterliegen oft Normen wie:
- DIN EN 14420: Norm für Schlaucharmaturen in der Industrie.
- ISO-Normen: Internationale Standards für Abmessungen und Sicherheitsanforderungen.
- SAE J516: Standards für Hydraulikarmaturen in der Automobilindustrie.
Die Lebensdauer kann verlängert werden durch:
- Regelmäßige Inspektion: Periodische Überprüfung auf Abnutzung und Beschädigungen.
- Verwendung geeigneter Materialien: Materialien sollten auf das Medium und die Umweltbedingungen abgestimmt sein.
- Korrekter Einbau: Sorgfältige Installation nach den Herstellerangaben
Rohrverschraubungen
Rohrverschraubungen sind mechanische Verbindungselemente, die Rohre sicher und dicht miteinander verbinden. Sie werden häufig in Rohrleitungssystemen für Flüssigkeiten und Gase verwendet, um flexible und lösbare Verbindungen zu schaffen.
Es gibt verschiedene Typen von Rohrverschraubungen, darunter:
- Klemmverschraubungen: Nutzen Klemmringe zur Abdichtung.
- Flanschverschraubungen: Bieten eine Verbindung über Flansche und Bolzen.
- Pressverschraubungen: Werden durch Verpressen am Rohr befestigt.
- Gewindeverschraubungen: Verwenden ein Schraubengewinde für die Verbindung.
Die Auswahl hängt ab von:
- Rohrmaterial: Die Verschraubung muss kompatibel mit dem Material des Rohres sein.
- Anwendungsbedingungen: Druck, Temperatur und Medium spielen eine Rolle.
- Rohrdurchmesser: Die Verschraubung muss für den spezifischen Durchmesser geeignet sein.
Wichtige Normen und Standards sind:
- DIN EN 10241: Standards für Gewindefittings aus Stahlguss.
- ISO 8434: Standards für Flanschverschraubungen.
- ASME B16.11: Standards für Schmiedefittings und Gewindefittings.
Für die Installation sollten folgende Schritte beachtet werden:
- Rohr vorbereiten: Das Rohrende muss sauber und frei von Graten sein.
- Dichtmittel verwenden: Bei Gewindeverschraubungen sollte ein geeignetes Dichtmittel oder Dichtband verwendet werden.
- Verschraubung festziehen: Die Verschraubung sollte fest, aber nicht übermäßig angezogen werden, um eine gute Dichtung zu gewährleisten.
Häufige Probleme umfassen:
- Leckagen: Oft verursacht durch unzureichende Dichtung oder Überbeanspruchung.
- Korrosion: Besonders bei unsachgemäßer Materialwahl für die Umgebung.
- Lockern: Durch Vibrationen oder ungenügendes Festziehen der Verschraubung.
Um Probleme zu vermeiden:
- Regelmäßig überprüfen: Inspektionen helfen, frühzeitig Abnutzung oder Schäden zu erkennen.
- Richtige Materialien: Materialien wählen, die für die spezifischen Bedingungen geeignet sind.
- Sorgfältige Installation: Der Montageanleitung des Herstellers folgen und geeignete Werkzeuge verwenden.
Rohrleitungen
Rohrleitungen sind Systeme aus Rohren, die zur Beförderung von Flüssigkeiten, Gasen oder Feststoffen verwendet werden. Sie kommen in zahlreichen Anwendungen zum Einsatz, darunter in der Industrie, im Bauwesen und in der Wasserversorgung.
Gerade Abschnitte und 90°-Bögen sind einfacher zu montieren und zu warten. Diese Konfigurationen erleichtern die Planung, Installation und Reinigung der Rohrsysteme. Außerdem minimieren sie den Druckverlust im Vergleich zu schrägen oder stark gekrümmten Leitungen.
Molchen ist die Reinigung von Rohrleitungen mit einem speziellen Gerät, dem Molch. Dieses Verfahren entfernt Ablagerungen und sorgt für eine effiziente Wartung, insbesondere in langen oder verwinkelten Rohrsystemen.
Druckverlust tritt auf, wenn sich Flüssigkeiten oder Gase durch eine Rohrleitung bewegen. Er wird durch Reibung, Änderungen des Durchmessers und Hindernisse verursacht. Die Berechnung des Druckverlusts ist wichtig, um sicherzustellen, dass die Rohrleitung den erforderlichen Druck und Durchfluss aufrechterhalten kann.
Typische Materialien für Rohrleitungen umfassen Stahl, Edelstahl, Kupfer, Kunststoff (z. B. PVC, PE), und Gusseisen. Die Wahl des Materials hängt von der Anwendung, den zu transportierenden Medien und den betrieblichen Bedingungen ab.
Die Inspektion hilft dabei, Lecks, Korrosion, Ablagerungen und andere Probleme frühzeitig zu erkennen, um Ausfälle zu vermeiden und die Lebensdauer der Rohrleitung zu verlängern. Regelmäßige Wartung und Überwachung sind entscheidend für den sicheren Betrieb von Rohrleitungssystemen.
In CAD-Software werden Rohrleitungen oft als “Leitungssegmente” mit spezifischen Verbindungsstücken und Zubehörteilen definiert. Diese Segmente erleichtern die Erstellung genauer Stücklisten für die Fertigung und Montage.
Rohrendenbearbeitung
Die Rohrendenbearbeitung umfasst alle Verfahren, die zur Bearbeitung und Anpassung der Enden von Rohren eingesetzt werden. Typische Methoden sind Anfasen, Kalibrieren, Bördeln und das Anbringen von Gewinden, um die Enden für die Montage vorzubereiten oder spezielle Funktionen zu ermöglichen.
Zu den gängigen Verfahren zählen:
- Anfasen: Abschrägen der Rohrkanten zur Vorbereitung auf das Schweißen.
- Kalibrieren: Herstellen eines genauen Rohrdurchmessers.
- Bördeln: Aufweiten des Rohrendes, oft zur Verbindung mit anderen Bauteilen.
- Gewindeschneiden: Erzeugen eines Gewindes am Rohrende für Schraubverbindungen
Die Rohrendenbearbeitung verbessert die Passgenauigkeit und Dichtheit von Verbindungen, erleichtert die Montage und sorgt für sichere und funktionelle Rohrsysteme. Sie ist besonders wichtig in Anwendungen, die hohe Präzision und Zuverlässigkeit erfordern, wie in der Hydraulik und Pneumatik.
Maschinen zur Rohrendenbearbeitung können je nach Verfahren variieren und umfassen Rohrsägen, Anfasmaschinen, Kalibriergeräte, Bördelmaschinen und Gewindeschneidgeräte. Einige moderne Systeme verwenden Laser für besonders präzise Schnitte und Formen.
Die Laserbearbeitung ermöglicht eine hohe Präzision und Wiederholgenauigkeit, minimiert Materialverluste und reduziert die Nachbearbeitungszeiten. Sie ist besonders nützlich für komplexe Formen und feine Details.
Eine sorgfältige Rohrendenbearbeitung trägt zur Gesamtqualität des Rohrsystems bei, indem sie eine bessere Passgenauigkeit und Dichtheit sicherstellt. Dies führt zu höheren Betriebssicherheiten und einer längeren Lebensdauer des Systems.
Die Bearbeitung muss oft spezifischen Normen und Standards entsprechen, die die Toleranzen, die Oberflächenqualität und die geometrischen Anforderungen der bearbeiteten Rohrenden festlegen. Diese Normen garantieren die Kompatibilität und Zuverlässigkeit in technischen Anwendungen.
Rohrbögen
Rohrbögen sind spezielle Fittings, die verwendet werden, um Richtungsänderungen in Rohrleitungen zu ermöglichen. Sie verbinden gerade Rohrabschnitte miteinander und werden in verschiedenen Winkeln, z. B. 45° oder 90°, hergestellt.
Rohrbögen bestehen häufig aus den gleichen Materialien wie die Rohrleitungen selbst, wie z. B. Stahl, Edelstahl, Kupfer, Kunststoff oder Gusseisen. Die Wahl des Materials hängt von der Anwendung und den zu transportierenden Medien ab.
In CAD-Software wie SOLIDWORKS oder AutoCAD Plant 3D können Rohrbögen angepasst oder neu erstellt werden, um den spezifischen Anforderungen einer Installation gerecht zu werden. Dies kann durch Ändern der Biegewinkel oder der Geometrie des Bogens erfolgen.
Rohrbögen sind unerlässlich, um Rohrleitungen um Hindernisse herumzuführen oder um die Richtung des Rohrverlaufs zu ändern. Sie ermöglichen flexible Layouts und Anpassungen an bauliche Gegebenheiten, was die Installation und den Betrieb von Rohrsystemen erheblich erleichtert.
Rohrbögen erhöhen den Druckverlust in Rohrleitungen aufgrund der zusätzlichen Reibung und Turbulenz, die durch die Richtungsänderung entstehen. Die genaue Auswirkung hängt von Faktoren wie dem Winkel des Bogens und der Geschwindigkeit des Mediums ab.
Benutzerdefinierte Rohrbögen werden speziell für bestimmte Anwendungen oder besondere Einbausituationen angefertigt, wenn Standardbögen nicht geeignet sind. Sie bieten Flexibilität in der Gestaltung und Anpassung von Rohrleitungssystemen.
Rohrbögen müssen verschiedenen industriellen Standards und Spezifikationen entsprechen, um die Kompatibilität mit den übrigen Rohrsystemen zu gewährleisten. Diese Standards definieren Parameter wie Biegewinkel, Durchmesser und Wandstärke.